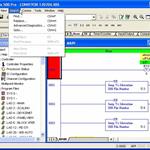
Update Required
To play the media you will need to either update your browser to a recent version or update your

Update Required
To play the media you will need to either update your browser to a recent version or update your
RSLogix500 Inserting Instructions
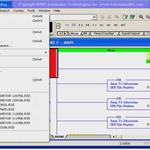
Update Required
To play the media you will need to either update your browser to a recent version or update your
RSLogix500 Opening a File

Update Required
To play the media you will need to either update your browser to a recent version or update your
RSLogix500 Creating a Project
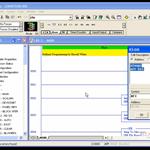
Update Required
To play the media you will need to either update your browser to a recent version or update your
RSLogix500 Instruction Comments
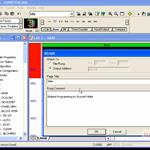
Update Required
To play the media you will need to either update your browser to a recent version or update your
RSLogix500 Rung Comments Page Titles
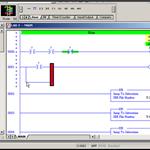
Update Required
To play the media you will need to either update your browser to a recent version or update your
RSLogix500 Inserting Branches
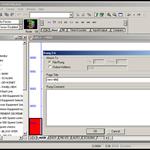
Update Required
To play the media you will need to either update your browser to a recent version or update your
RSLogix500 Program Organization, Part 1 - Overview
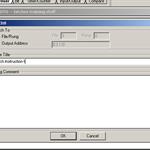
Update Required
To play the media you will need to either update your browser to a recent version or update your
RSLogix500 Program Organization, Part 2 - Examples
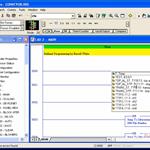
Update Required
To play the media you will need to either update your browser to a recent version or update your
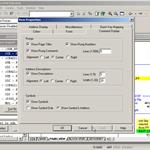
Update Required
To play the media you will need to either update your browser to a recent version or update your
RSLogix500 View Properties
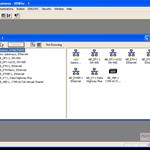
Update Required
To play the media you will need to either update your browser to a recent version or update your

Update Required
To play the media you will need to either update your browser to a recent version or update your
RSLogix500 Online Offline
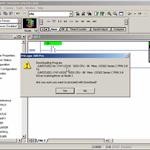
Update Required
To play the media you will need to either update your browser to a recent version or update your
RSLogix500 Dowloading and Uploading
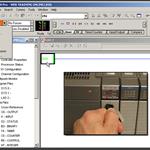
Update Required
To play the media you will need to either update your browser to a recent version or update your
RSLogix500 Processor Modes
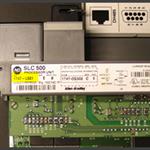
Update Required
To play the media you will need to either update your browser to a recent version or update your
RSLogix500 Processor and Cards
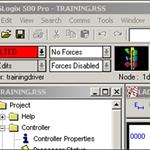
Update Required
To play the media you will need to either update your browser to a recent version or update your
RSLogix500 Introduction to Faults
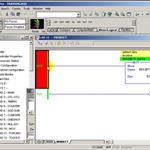
Update Required
To play the media you will need to either update your browser to a recent version or update your
RSLogix500 Indirect Addressing
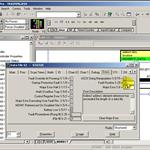
Update Required
To play the media you will need to either update your browser to a recent version or update your
RSLogix500 Indirect Addressing Faults
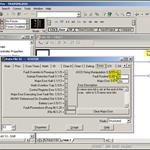
Update Required
To play the media you will need to either update your browser to a recent version or update your
RSLogix500 Handling Faults
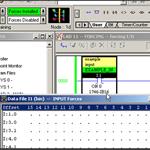
Update Required
To play the media you will need to either update your browser to a recent version or update your
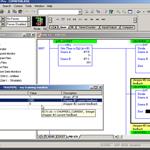
Update Required
To play the media you will need to either update your browser to a recent version or update your
RSLogix500 Custom Data Monitor
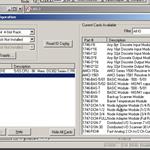
Update Required
To play the media you will need to either update your browser to a recent version or update your
RSLogix500 I/O Configuration
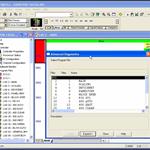
Update Required
To play the media you will need to either update your browser to a recent version or update your
RSLogix500 Advanced Diagnostics
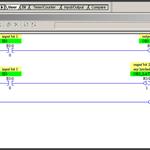
Update Required
To play the media you will need to either update your browser to a recent version or update your
RSLogix500 Instructions OTL OTU, Part 1
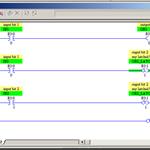
Update Required
To play the media you will need to either update your browser to a recent version or update your
RSLogix500 Instructions OTL OTU, Part 2
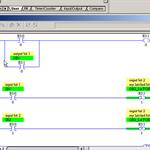
Update Required
To play the media you will need to either update your browser to a recent version or update your
RSLogix500 Instructions OTL OTU, Part 3
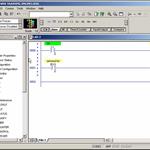
Update Required
To play the media you will need to either update your browser to a recent version or update your
RSLogix500 Instructions, OTE
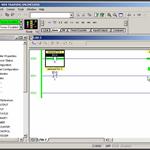
Update Required
To play the media you will need to either update your browser to a recent version or update your
RSLogix500 Instructions, XIC XIO
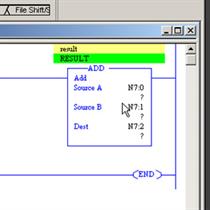
Update Required
To play the media you will need to either update your browser to a recent version or update your
RSLogix500 Instructions, ADD
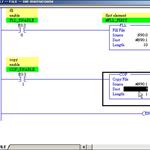
Update Required
To play the media you will need to either update your browser to a recent version or update your
RSLogix500 Instructions, COP
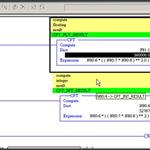
Update Required
To play the media you will need to either update your browser to a recent version or update your
RSLogix500 Instructions, CPT - Part 2
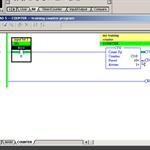
Update Required
To play the media you will need to either update your browser to a recent version or update your
RSLogix500 Instructions, CTU CTD - Part 1
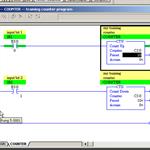
Update Required
To play the media you will need to either update your browser to a recent version or update your
RSLogix500 Instructions, CTU CTD - Part 2
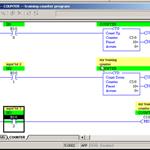
Update Required
To play the media you will need to either update your browser to a recent version or update your
RSLogix500 Instructions, CTU CTD - Part 3
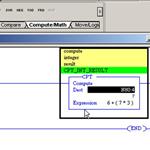
Update Required
To play the media you will need to either update your browser to a recent version or update your
RSLogix500 Instructions, CPT - Part 1
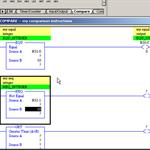
Update Required
To play the media you will need to either update your browser to a recent version or update your
RSLogix500 - Comparison - Part1
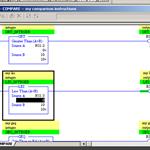
Update Required
To play the media you will need to either update your browser to a recent version or update your
RSLogix500 - Comparison - Part 2
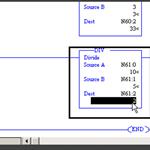
Update Required
To play the media you will need to either update your browser to a recent version or update your
RSLogix500 Instructions, DIV
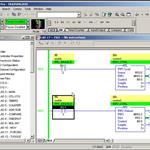
Update Required
To play the media you will need to either update your browser to a recent version or update your
RSLogix500 - FIFO - FFL and FFU - Part 1
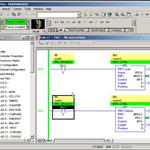
Update Required
To play the media you will need to either update your browser to a recent version or update your
RSLogix500 - FIFO - FFL and FFU - Part 2
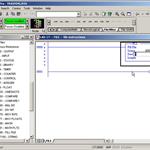
Update Required
To play the media you will need to either update your browser to a recent version or update your
RSLogix500 Instructions, FLL
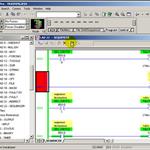
Update Required
To play the media you will need to either update your browser to a recent version or update your
RSLogix500 Instructions, JMP and LBL
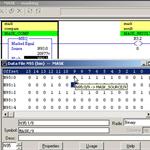
Update Required
To play the media you will need to either update your browser to a recent version or update your
RSLogix500 Instructions, Masking and MEQ
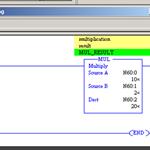
Update Required
To play the media you will need to either update your browser to a recent version or update your
RSLogix500 Instructions, MUL
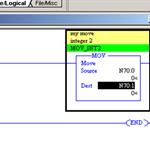
Update Required
To play the media you will need to either update your browser to a recent version or update your
RSLogix500 Instructions, MOV
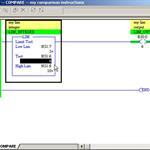
Update Required
To play the media you will need to either update your browser to a recent version or update your
RSLogix500 Instructions, LIM
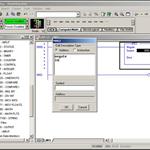
Update Required
To play the media you will need to either update your browser to a recent version or update your
RSLogix500 Instructions, NEG
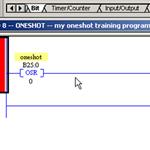
Update Required
To play the media you will need to either update your browser to a recent version or update your
RSLogix500 Instructions, OSR
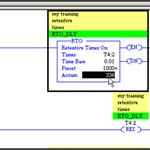
Update Required
To play the media you will need to either update your browser to a recent version or update your
RSLogix500 Instructions, RTO
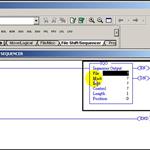
Update Required
To play the media you will need to either update your browser to a recent version or update your
RSLogix500 Instructions, SQO sequencer - Part 1 of 3
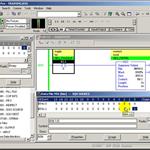
Update Required
To play the media you will need to either update your browser to a recent version or update your
RSLogix500 Instructions, SQO sequencer - Part 2 of 3
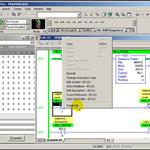
Update Required
To play the media you will need to either update your browser to a recent version or update your
RSLogix500 Instructions, SQO sequencer - Part 3 of 3
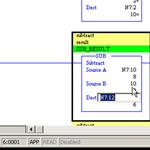
Update Required
To play the media you will need to either update your browser to a recent version or update your
RSLogix500 Instructions, SUB
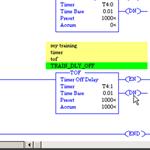
Update Required
To play the media you will need to either update your browser to a recent version or update your
RSLogix500 Instructions, TOF
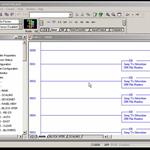
Update Required
To play the media you will need to either update your browser to a recent version or update your
RSLogix500 Instructions, JSR and RET
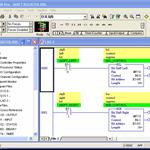
Update Required
To play the media you will need to either update your browser to a recent version or update your
RSLogix500 Shift registers
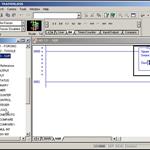
Update Required
To play the media you will need to either update your browser to a recent version or update your
RSLogix500 Instructions, SQR
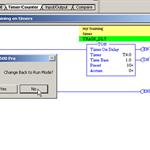
Update Required
To play the media you will need to either update your browser to a recent version or update your
RSLogix500 Instructions, TON - Part 1
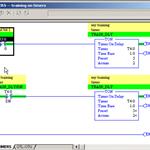
Update Required
To play the media you will need to either update your browser to a recent version or update your
RSLogix500 Instructions, TON - Part 2
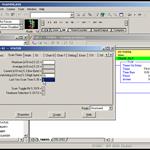
Update Required
To play the media you will need to either update your browser to a recent version or update your
RSLogix500 Instructions, TON - Part 3
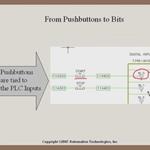
Update Required
To play the media you will need to either update your browser to a recent version or update your
Introduction to Ladder Logic